Abstract
Despite its rich history and cultural significance, Indian handblock printing faces a challenge in reaching younger audiences. In an age of fast fashion and mass production, many young people are unaware of the beauty and value of handcrafted textiles. There is a need to educate and engage young consumers about the art of handblock printing, highlighting its sustainable and ethical aspects.
Despite its rich history and cultural significance, Indian handblock printing faces a challenge in reaching younger audiences. In an age of fast fashion and mass production, many young people are unaware of the beauty and value of handcrafted textiles. There is a need to educate and engage young consumers about the art of handblock printing, highlighting its sustainable and ethical aspects.
Glitch Textiles explores the fusion of contemporary art form Glitch art with Indian traditional Sanganeri hand block printing on textiles to promote the craft among young people. I drew inspiration from various artists and designs, experimenting with different fabrications to create a range of garments suitable for today's youth. These garments blend contemporary style with a modern twist, preserving traditional roots while offering a fresh and innovative look. Embracing the concept of "Imperfection is Beautiful," the fusion of Glitch art and Sanganeri hand block printing not only revitalizes the traditional craft but also celebrates the beauty of flaws, bridging the gap between heritage and modernity in the world of fashion.
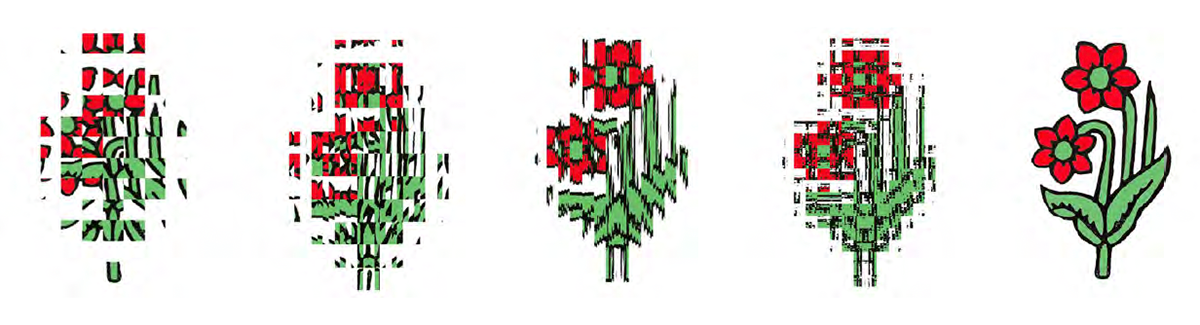
Declaration
I hereby declare that the project work entitled- “Glitch textiles: creating imperfections” submitted to Pearl Academy is work done by me under the guidance of textile faculty members for the cohort 2013-2017. This project work is not submitted to any other university or institute for any other form of degree or diploma.
I hereby declare that the project work entitled- “Glitch textiles: creating imperfections” submitted to Pearl Academy is work done by me under the guidance of textile faculty members for the cohort 2013-2017. This project work is not submitted to any other university or institute for any other form of degree or diploma.
Mrs. Sakshi Paul Babbar
(Faculty - Textile Department, Pearl Academy)
Mentor
(Faculty - Textile Department, Pearl Academy)
Mentor
Khushboo Kaur
TDFI Level-III
TDFI Level-III
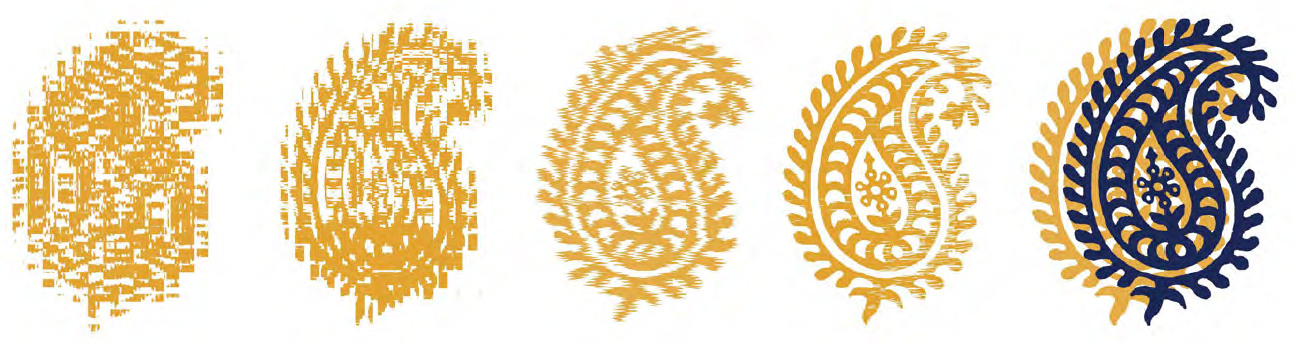
Concept Brief
As a textile designer, I find beauty in imperfection and seek to celebrate it through my work. My fascination with glitch art, first introduced during an internship under mentor Ashutosh Badone, sparked a creative journey to blend this modern art form with the traditional craft of Sanganeri block printing.
As a textile designer, I find beauty in imperfection and seek to celebrate it through my work. My fascination with glitch art, first introduced during an internship under mentor Ashutosh Badone, sparked a creative journey to blend this modern art form with the traditional craft of Sanganeri block printing.
Glitch art, characterized by the intentional use of digital and analog errors for aesthetic purposes, resonates with me as it embodies the beauty found in imperfections. In my quest for innovation, I envisioned a fusion of glitch art and Sanganeri block printing, where I could create and enhance glitches in printing processes.
With a focus on surface printing and embellishment, I embarked on this fusion for my graduation project, confident in my abilities to merge these distinct art forms. Drawing inspiration from designers like Faig Ahmed and Philip David Stearns, who have successfully integrated glitch art with their cultures and styles, I also drew from my own cultural heritage of Sanganeri Traditional Block Printing.
In my work, I aim to contemporarize the traditional look of block printing by creating and enhancing errors and defects in Sanganeri block print motifs. Through techniques such as block printing and screen printing, I strive to showcase the beauty of imperfection in textiles, creating unique and innovative pieces that celebrate the fusion of art and tradition.
SANGANERI BLOCK PRINTING
-The Traditional Handicraft of Sanganer, Rajasthan
-The Traditional Handicraft of Sanganer, Rajasthan
About Sanganeri Block Printing
Historically renowned for block printing, the bustling town of Sanganer evokes an almost mythical association with hand-printed cloth. Home to a large community of block printers for centuries, the city remains a viral contributor to India’s vibrant textile industry even though time has brought significant changes. A place where ancient traditions collide with modern concerns, Sanganer presents an interesting paradigm of historic Sanganeri fabric with contemporary prints reveals differences that, in turn, illustrate the evolution of block printing in Sanganer.Traditionally, the cohesive community of Sanganeri chhippa printers andrangrez dyers worked together in harmony using hand carved blocks, natural dyes and classic motifs. By the 20th century, the increasing reliance on screen printing and chemical colours ruptured this ancient dynamic and fostered the high-volume production of modern textiles.
According to the 2008 Sanganer census, 423 screen printing units far exceed the 350 block printing units in both number and size which exemplifies the town’s rapid transformation since 1947. This development has not only affected the role of craftspeople, but also resulted in the modification of classic designs to suit contemporary taste.
Indian artisans have always displayed an amazing resilience and hand block printing has continually adapted to market forces in India and beyond. During the 18th century, the famed chhippa and rangrez communities of Sanganer expanded their trade by uniting to create delicately patterned and coloured muslin material for a broad- based clientele. Royal patronage fuelled domestic trade and eventually launched the work of the Sanganeri prints was highly prized. Towards the end of the late 19th century mechanization, accomplished by the introduction of chemical dyestuffs, resulted in competition from labour intensive processes emerging in the West. The ability to create chemically coloured, machine-woven and roller-printed fabrics significantly reduced production costs. By the late 1950s, Sanganer printers faced a drastic decline indemand for their textiles
Geography
Sanganer began as a sleepy village located on the edge of a broad riverbank in the Dhundhar region of Rajputana now known as Rajasthan. Topographically Sanganer was located on prime, fertile land at the bend of the Aman-i-shah river. Although dams upstream now restrict the flow of water, older residents of Sanganer still call the former river course Saraswati Nadi. Sanganer flourished with a large community of mali gardeners who cultivated vegetables and flowers in the alluvial soils by the water’s edge.
During the 11th century Kachchwaha Rajputs migrated to the area around Jaipur where they defeated the indigenous Minas and established Amber, or Amer, as a military fortification and capital. From the 14th century onward clans of Rajput nobles created states of which the most prominent became Bikaner, Jaipur, Bharatpur and Dholpur on the eastern edge of Rajputana and Afghan adventurers created Tonk, the only Muslim state. The Kanchchwaha Rajput Price Sangaji founded Sanganer in the 16th century. He established the fortified town as the tensil or administrative centre of the sub-district. Sanganer was thriving by the 17th century partially due to its strategic location along the major trade routes. The northern road led to Amer while the Mughal imperial highway stretched past Sanganer from east to west, linking the powerful city of Agra to the Islamic stronghold of Ajmer and the seaports of Gujarat on the Indian Ocean.
Reminders of Sanganer’s architectural heritage are still visible in the older quarters. Remnants of crenellated walls with gateways surround primarily 17th century public buildings and private havelis mansions located within the crumbling ramparts. Shikara spires of Sri Digamber Mandir dominate Sanganer’s skyline while intricate carvings embellish the Jain temple’s interior. Although it is uncertain when different construction phases began, a date etched into a pylon suggests the completion of the mandir in the 10th century AD. Relocation of the Digamber’s sect’s ancient monastic order, Mula Sangh, enhanced Sanganer’s reputation and increased the population during the 17th century. Due to the bhattarakas leaders careful stewardship and fiscal acumen, Sri Digamber Mandir remains a jewel on the Jain pilgrimage route and continues to welcome visitors today.
In 1727 Maharaja Jai Singh moved the capital from Amber in the Aravalli foothills to his new city of Jaipur situated on the plains below. The ruler recognized the importance of relocating close to Sanganer and established trade routes. In turn Sanganer enjoyed increased activity because of its proximity to the bustling, new city. From then on Sanganeri’s fate became entwined with integrated into Rajasthan with Jaipur as the capital, Sanganer rapidly evolved from a satellite town into an industrial suburb of this expanding city.
Sanganer began as a sleepy village located on the edge of a broad riverbank in the Dhundhar region of Rajputana now known as Rajasthan. Topographically Sanganer was located on prime, fertile land at the bend of the Aman-i-shah river. Although dams upstream now restrict the flow of water, older residents of Sanganer still call the former river course Saraswati Nadi. Sanganer flourished with a large community of mali gardeners who cultivated vegetables and flowers in the alluvial soils by the water’s edge.
During the 11th century Kachchwaha Rajputs migrated to the area around Jaipur where they defeated the indigenous Minas and established Amber, or Amer, as a military fortification and capital. From the 14th century onward clans of Rajput nobles created states of which the most prominent became Bikaner, Jaipur, Bharatpur and Dholpur on the eastern edge of Rajputana and Afghan adventurers created Tonk, the only Muslim state. The Kanchchwaha Rajput Price Sangaji founded Sanganer in the 16th century. He established the fortified town as the tensil or administrative centre of the sub-district. Sanganer was thriving by the 17th century partially due to its strategic location along the major trade routes. The northern road led to Amer while the Mughal imperial highway stretched past Sanganer from east to west, linking the powerful city of Agra to the Islamic stronghold of Ajmer and the seaports of Gujarat on the Indian Ocean.
Reminders of Sanganer’s architectural heritage are still visible in the older quarters. Remnants of crenellated walls with gateways surround primarily 17th century public buildings and private havelis mansions located within the crumbling ramparts. Shikara spires of Sri Digamber Mandir dominate Sanganer’s skyline while intricate carvings embellish the Jain temple’s interior. Although it is uncertain when different construction phases began, a date etched into a pylon suggests the completion of the mandir in the 10th century AD. Relocation of the Digamber’s sect’s ancient monastic order, Mula Sangh, enhanced Sanganer’s reputation and increased the population during the 17th century. Due to the bhattarakas leaders careful stewardship and fiscal acumen, Sri Digamber Mandir remains a jewel on the Jain pilgrimage route and continues to welcome visitors today.
In 1727 Maharaja Jai Singh moved the capital from Amber in the Aravalli foothills to his new city of Jaipur situated on the plains below. The ruler recognized the importance of relocating close to Sanganer and established trade routes. In turn Sanganer enjoyed increased activity because of its proximity to the bustling, new city. From then on Sanganeri’s fate became entwined with integrated into Rajasthan with Jaipur as the capital, Sanganer rapidly evolved from a satellite town into an industrial suburb of this expanding city.
Historical background
The Sanganer town of Jaipur State must, however, be regarded as the very metropolis of the calico-printing craft of India so far as art conceptions and techniques are concerned. (Sir George Watt 1903:247) Before the 17th century, historical accounts only mention the town of Sanganer as a source of finely dyed or bleached cottons. The wide sandy riverbanks offered space to spread out the cloth in the bright sunshine, while its clean mineral-rich water was perfect for processing dyes. Sanganer prospered during the 18th century with the growth of a hand-block printing community which transformed the town into a prominent centre of textile printing.
The origin of the printing craft in Sanganer prior to the establishment of Jaipur is speculative. Some Hindu block printers claim their forebears arrived from Gujarat and historical records support this claim. The social upheavals that occurred during the wars of Mughal Emperor Aurangzeb during the late-17th century, followed by incursions of raiding Marathas, may have forced Gujarati printers to flee to Sanganer. The flow of ideas between Gujarat and Rajasthan fostered aesthetic similarities marked by the clear, bold lines appearing in both state’s printing styles. (Irwin & Hall 1971:111)
The origin of the printing craft in Sanganer prior to the establishment of Jaipur is speculative. Some Hindu block printers claim their forebears arrived from Gujarat and historical records support this claim. The social upheavals that occurred during the wars of Mughal Emperor Aurangzeb during the late-17th century, followed by incursions of raiding Marathas, may have forced Gujarati printers to flee to Sanganer. The flow of ideas between Gujarat and Rajasthan fostered aesthetic similarities marked by the clear, bold lines appearing in both state’s printing styles. (Irwin & Hall 1971:111)
As Jaipur’s population grew the commercial areas became increasingly congested and craftsmen spilled outside of the confining city walls. Oral tradition suggests that the Chhippa families of Jaipur began to shift their work to locations where space and running water were freely available, yet still within easy reach of the capital. The riverbanks of Sanganer presented the ideal new location with the added benefit of specialist dyers and cloth bleachers residing in the town. These artisans formed a large, supportive community with block printing at the core of their culture.
Initially, the chhippas of Jaipur brought their cloth bundles to the river in Sanganer every day and returned home at nightfall after finishing their work. As the quantity of work increased, these craftsmen would spend several nights or longer in Sanganer. The printing process was still completed inside their city homes, often by the women of the family; but, the labour-intensive dhobi work of washing, bleaching and rinsing the heavy bundles of cloth happened along the river. Today many of the chhippa families living in Sanganer are descendants of those who relocated from Jaipur over four or five generations ago.
Original textile products of Sanganer were roughly divided into three categories. First, the syahi-begar black and red designs on the gossamer white cloth were worn as Safa turbans or angochha shawls by men of the local community. Second, butis sprigged floral motifs stamped upon softly coloured or white backgrounds graced Jaipur court society. Third, dupatta shawls bearing auspicious red designs on a Sanganer’s location on the trade routes enhanced the possibility of exposure to fresh ideas along with the exchange of such goods. As purveyors of textiles to the royal courts and later to the haat markets in Jaipur, Sanganeri craftspeople entered the realms of international trade by the 19th century. Foreign influences stemming from far-flung commissions gradually inspired the designs offered to local customers. Ultimately this new repertoire of popular prints perpetuated the fame of the Sanganeri artisans, exemplifying the beauty and skill of their work.
Block Carving
A critical component of block printing is block carving. This stamp underpins the work of every chhippa and is an art form itself. The block carving community of Santander is often overlooked yet these small businesses illustrate the shifting dynamics of Sanganer’s textile industry. Historically block carvers worked from a repertoire of designs designated to a particular community. As the old blocks aged from repetitive use they were mended or replaced with fresh blocks bearing the same classic motifs. Close proximity between the carvers and printers was unnecessary and at times hundreds of miles divided these craftspeople.
A critical component of block printing is block carving. This stamp underpins the work of every chhippa and is an art form itself. The block carving community of Santander is often overlooked yet these small businesses illustrate the shifting dynamics of Sanganer’s textile industry. Historically block carvers worked from a repertoire of designs designated to a particular community. As the old blocks aged from repetitive use they were mended or replaced with fresh blocks bearing the same classic motifs. Close proximity between the carvers and printers was unnecessary and at times hundreds of miles divided these craftspeople.
Until the 20th century local families of block carvers lived mainly in the Purani Basti district of Jaipur’s walled city. Very few families based themselves in Sanganer. Those who did live there tended to be carvers who mended old blocks rather than those who created new blocks. Then in the late 1970s, the number of traditional carvers and printers in Sanganer grew following an exodus of artisans from Farrukhabad. Suffering from the pressure of competing with modern printing methods, these migrant craftspeople looked to Sanganer and Jaipur to provide sustainable employment.
By the end of 1980s organized borders of butah and buti combinations gave way to stripes, geometric and irregular bold repeats. In order to compete with screen printing, the size of the blocks has increased by three to four times from their original size.
According to the 2009 census there are 152 block carving units in Sanganer today. They receive regular orders from local printing units but their numbers are shrinking in conjunction with the block printers.
Every carver retains a traditional tool kit: a personal and unique set of over thirty miniature chisels, well-worn hammers, and old fashioned bow-drills. The symbolic relationship between the art of hand carving wooden blocks and the skill of printing is now ingrained in the heart of Sanganer. Old and new designs sit side-by-side.
Block printing
The traditional printing process began with a rigorous scouring and bleaching procedure called Teluni, to emulsify the oils on the cotton threads.
The cloth was treated with Harda, which functions as a pre-mordant link between the fibres and the various other ingredients. It left a yellowish tinge to the fabric, hence known as ‘pila-karna‘. The craftsman then printed the black area of the design using the Syahi (ink) printing paste prepared using scrap iron, horseshoes and Gur (jaggery) in an earthenware vessel. After the black outline was made, the craftsman made the Begar, a mordant used for red. Alum was mixed with sticky tree gum paste and a pinch of Geru red ochre to bring out colour in the otherwise transparent paste. The begar paste was then applied using a ‘Datta’ block to fill in the ‘Rekh’ (the outlining block) and the fabric was dried for a week.
The fabric had to be thoroughly washed in order toremove the tree gum. The next step known as Ghan ki Rangai involves use of a copper vessel ‘Tamda’ on a Bhatti. Red dye matter along with Shakur ka phool or dhaura ka phool was added with drop of castor or sesame oil. The printer washed the dyed fabric in the running river water and allowed to dry in the scorching sun with sprinkling of water time to time. This resulted in a bright white background and clear richly coloured butis and butahs.
The traditional printing process began with a rigorous scouring and bleaching procedure called Teluni, to emulsify the oils on the cotton threads.
The cloth was treated with Harda, which functions as a pre-mordant link between the fibres and the various other ingredients. It left a yellowish tinge to the fabric, hence known as ‘pila-karna‘. The craftsman then printed the black area of the design using the Syahi (ink) printing paste prepared using scrap iron, horseshoes and Gur (jaggery) in an earthenware vessel. After the black outline was made, the craftsman made the Begar, a mordant used for red. Alum was mixed with sticky tree gum paste and a pinch of Geru red ochre to bring out colour in the otherwise transparent paste. The begar paste was then applied using a ‘Datta’ block to fill in the ‘Rekh’ (the outlining block) and the fabric was dried for a week.
The fabric had to be thoroughly washed in order toremove the tree gum. The next step known as Ghan ki Rangai involves use of a copper vessel ‘Tamda’ on a Bhatti. Red dye matter along with Shakur ka phool or dhaura ka phool was added with drop of castor or sesame oil. The printer washed the dyed fabric in the running river water and allowed to dry in the scorching sun with sprinkling of water time to time. This resulted in a bright white background and clear richly coloured butis and butahs.
Motifs
The ‘Syahi Begar’ black and red designs on gossamer white cloth adorned the Safa turbans or Angochha shawls of men of the local community. Buti sprigged floral motifs stamped upon softly coloured or white backgrounds graced Jaipur court society. Many chhipas in Sanganer remember the regular production of printed designs for local women. Some patterns mimicked the Bandhani (tie-dyed) head cloths particular to local Mali and Mina women. The bright yellow Mali chunnari or veil cloth is distinctively patterned with a single large red circular motif in the center of the rectangular cloth. On the other hand, the Mina Chaddar, a heavy cotton shawl, is covered with small flower-shaped arrangements of simple red dots on a dark-black background.
The ‘Syahi Begar’ black and red designs on gossamer white cloth adorned the Safa turbans or Angochha shawls of men of the local community. Buti sprigged floral motifs stamped upon softly coloured or white backgrounds graced Jaipur court society. Many chhipas in Sanganer remember the regular production of printed designs for local women. Some patterns mimicked the Bandhani (tie-dyed) head cloths particular to local Mali and Mina women. The bright yellow Mali chunnari or veil cloth is distinctively patterned with a single large red circular motif in the center of the rectangular cloth. On the other hand, the Mina Chaddar, a heavy cotton shawl, is covered with small flower-shaped arrangements of simple red dots on a dark-black background.
Dupattas and shawls bearing auspicious red designs on a white or yellow background adorned the pious attendees at Hindu temples. Home furnishings incorporate a wealth of folk imagery. Regimented borders of flowers, vines, animals and human figures flank the geometric jaal patterns in the center. Ranks of small soldiers accompanied by decorated cows, elephants or horses compete with vignettes depicting popular folk tales.
Sanganeri Craft: Fading Into Extinction
In many ways, the story of Sanganer is a cautionary tale. Here one can truly feel the impact of modernization. While screen printing is on the road, the number of block printers is on the decline. The pressure to compete in the modern world is taking its toll. Screen printing is a speedier method of printing but spiritual complexities underpin block printing. The chhippa community shares inherited wisdom stemming from the past. The Sanganeri block print craft once popular for its traditional motifs and use of natural dyes is almost on the brink of extinction. The traditional motifs were exquisite and truly displayed an artisan’s creativity and skill. These motifs were inspired by nature such as floral motifs, the peacock or ‘Mor’motif, the ‘Keri’, the ‘Nimser’ etc. The traditional motifs have now been replaced by modern designs such as Stripes and Chevron.
Owing to the advent of digital screen printing technology through which artisans can churn out fabrics at a quicker pace leading to better profits, this craft is now being practised by only limited craftsmen. The use of traditional natural dyes too is being discontinued in favour of synthetic dyes, hence the Sanganeri as a culture needs urgent revival.
Printer's Tale
On my visit to Anokhi Museum, I met Salim Bhai who is a block printer at Anokhi. He shared his life story as a Block printer based in Sanganer.
“I have been printing for the last 30 years in Sanganer. I am originally from Farrukhabad, Uttar Pradesh. My father was called here by my uncle and offered a job as a chippa(printer). The culture of printing has been in my family for 3 generations. My father, me and now my son are following the tradition.
There are many changes which I feel have occurred in these 30 years. Earlier we used to do printing with natural dyes, now we have been introduced to chemical colours which are much easier and are quickly made. Very few printers today use natural dyes. It also depends on the market demand for natural dyes.
We used to work on smaller tables called pullia, but now we have huge tables on which more fabric can be placed. (When I asked him about the names allot to Sanganeri butah(block print motifs) and their usage nowadays) He said it’s been a while since people used the traditional butahs. Yes, many motifs have been stylized according to the market but the popular ones are still used with some other geometric compositions.”
Talking about Anokhi Museum, he said,” I consider it a good opportunity for me and a good platform for people to understand the printing crafts as a part of their own culture. Foreigners also find the craft very fascinating and appreciate our work.
On my visit to Anokhi Museum, I met Salim Bhai who is a block printer at Anokhi. He shared his life story as a Block printer based in Sanganer.
“I have been printing for the last 30 years in Sanganer. I am originally from Farrukhabad, Uttar Pradesh. My father was called here by my uncle and offered a job as a chippa(printer). The culture of printing has been in my family for 3 generations. My father, me and now my son are following the tradition.
There are many changes which I feel have occurred in these 30 years. Earlier we used to do printing with natural dyes, now we have been introduced to chemical colours which are much easier and are quickly made. Very few printers today use natural dyes. It also depends on the market demand for natural dyes.
We used to work on smaller tables called pullia, but now we have huge tables on which more fabric can be placed. (When I asked him about the names allot to Sanganeri butah(block print motifs) and their usage nowadays) He said it’s been a while since people used the traditional butahs. Yes, many motifs have been stylized according to the market but the popular ones are still used with some other geometric compositions.”
Talking about Anokhi Museum, he said,” I consider it a good opportunity for me and a good platform for people to understand the printing crafts as a part of their own culture. Foreigners also find the craft very fascinating and appreciate our work.
Anokhi: An Initiative
trip to the Amber Fort is a popular destination when touring Jaipur, but visitors are increasingly adding what critics have called ‘a little gem of a museum’ onto their list as well. In the Fort’s shadow and a mere ten-minute walk through the cobbled streets of Amber, the historic capital of Rajasthan, lies the Anokhi Museum of Hand Printing (AMHP). Located in a magnificently restored haveli or mansion, the museum displays a varied selection of block-printed textiles alongside images, tools and related objects – all chosen to provide an in-depth look into the complexity of this ancient tradition.
Like crafts worldwide, the block printing industry faces serious challenges trying to keep pace with modern manufacturing. The Anokhi Museum of Hand Printing addresses this fragile situation primarily through education. Dedicated to the art of block printing, AMHP strives to inform both textile specialists and the general public alike; but more importantly, the artisans themselves are encouraged to visit and view their craft in a unique and inspirational way. Hopefully, visitors from India and abroad will leave the museum a little wiser, and also more sensitive to the need to protect this enduring heritage craft for future generations.
The creation of the Anokhi Museum of Hand Printing was the initiative of Founder & Director, Rachel Bracken Singh and her husband Pritam Singh. Pritam’s father, John Singh, purchased the dilapidated Chanwar Palkiwon ki Haveli mansion in the late 1970s and began a 3-year renovation project in 1989. With the guidance of architects, Nimish Patel & Parul Zaveri, the building was restored to its original grandeur. By demonstrating the feasibility of using indigenous materials, time-honoured construction methods and skilled local craftsmen, the preservation project earned a UNESCO award for ‘Cultural Heritage Conservation’ in 2000.
A highlight of any visit is watching their daily block printing & block carving demonstrations. Here visitors have an opportunity to interact with artisans and try their hand at the craft. And their mini-auditorium to view our daily film program which features short documentaries and slide shows on a variety of related topics.
trip to the Amber Fort is a popular destination when touring Jaipur, but visitors are increasingly adding what critics have called ‘a little gem of a museum’ onto their list as well. In the Fort’s shadow and a mere ten-minute walk through the cobbled streets of Amber, the historic capital of Rajasthan, lies the Anokhi Museum of Hand Printing (AMHP). Located in a magnificently restored haveli or mansion, the museum displays a varied selection of block-printed textiles alongside images, tools and related objects – all chosen to provide an in-depth look into the complexity of this ancient tradition.
Like crafts worldwide, the block printing industry faces serious challenges trying to keep pace with modern manufacturing. The Anokhi Museum of Hand Printing addresses this fragile situation primarily through education. Dedicated to the art of block printing, AMHP strives to inform both textile specialists and the general public alike; but more importantly, the artisans themselves are encouraged to visit and view their craft in a unique and inspirational way. Hopefully, visitors from India and abroad will leave the museum a little wiser, and also more sensitive to the need to protect this enduring heritage craft for future generations.
The creation of the Anokhi Museum of Hand Printing was the initiative of Founder & Director, Rachel Bracken Singh and her husband Pritam Singh. Pritam’s father, John Singh, purchased the dilapidated Chanwar Palkiwon ki Haveli mansion in the late 1970s and began a 3-year renovation project in 1989. With the guidance of architects, Nimish Patel & Parul Zaveri, the building was restored to its original grandeur. By demonstrating the feasibility of using indigenous materials, time-honoured construction methods and skilled local craftsmen, the preservation project earned a UNESCO award for ‘Cultural Heritage Conservation’ in 2000.
A highlight of any visit is watching their daily block printing & block carving demonstrations. Here visitors have an opportunity to interact with artisans and try their hand at the craft. And their mini-auditorium to view our daily film program which features short documentaries and slide shows on a variety of related topics.
GLITCH ART
-The Modern Art
-The Modern Art
“Imperfection is beauty,
madness is genius and
it’s better to be absolutely ridiculous
than absolutely boring.” -Marilyn Monroe.
madness is genius and
it’s better to be absolutely ridiculous
than absolutely boring.” -Marilyn Monroe.
In a technical sense, a Glitch is the unexpected result of a malfunction. I have always believed that there’s a certain beauty of imperfection. Iman Moradi, the first official glitch theorist, has written extensively on the subject of glitch art beginning with his dissertation for the University of Huddersfield (PDF) until the publication of his recently released book Glitch: Designing Imperfections.
Moradi divides glitch art in two categories: The first is the pure glitch which is the result of a malfunction or error, an unpremeditated digital artifact. The second is the glitch-alike which is the result of an intentional decision on the user side. The classification of Pure Glitch and the Glitch-alike was conceived in response to this necessity.I simply proposed that Glitch-alikes are a collection of digital artefacts that resemble visual aspects of real glitches found in their original habitat.
Moradi divides glitch art in two categories: The first is the pure glitch which is the result of a malfunction or error, an unpremeditated digital artifact. The second is the glitch-alike which is the result of an intentional decision on the user side. The classification of Pure Glitch and the Glitch-alike was conceived in response to this necessity.I simply proposed that Glitch-alikes are a collection of digital artefacts that resemble visual aspects of real glitches found in their original habitat.
Pure Glitch, Accidental, Coincidental, Appropriated, Found, Real,
Glitch-alike, Deliberate, Planned, Created, Designed
Glitch-alike, Deliberate, Planned, Created, Designed
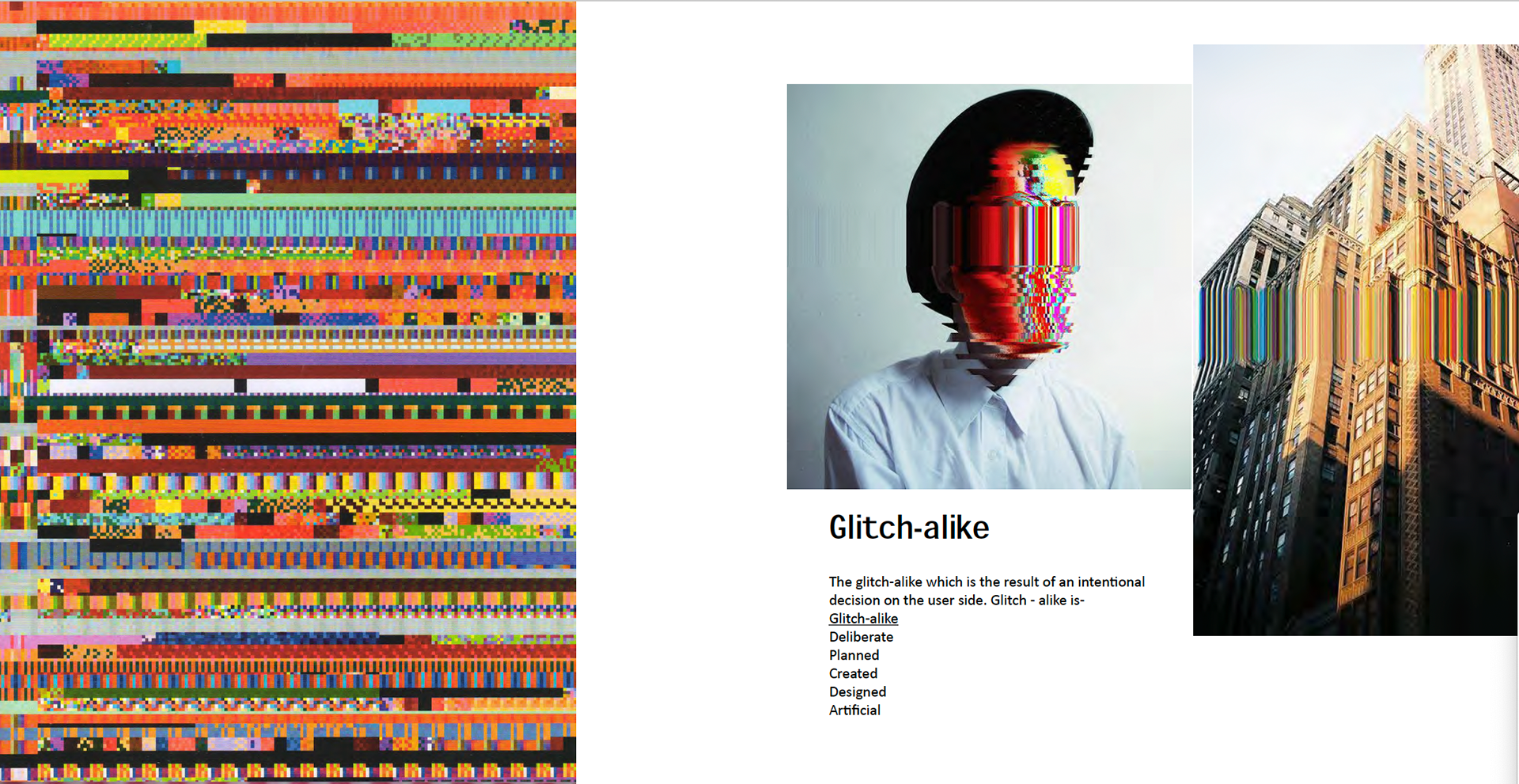
Artists and designers who inspire me for this fusion- Faig Ahmed, Philip David Stearns,
Benjamin (Berg-stallio!), Ferrucio Laviani, Nukeme and Ucnv
Benjamin (Berg-stallio!), Ferrucio Laviani, Nukeme and Ucnv
Faig Ahmed
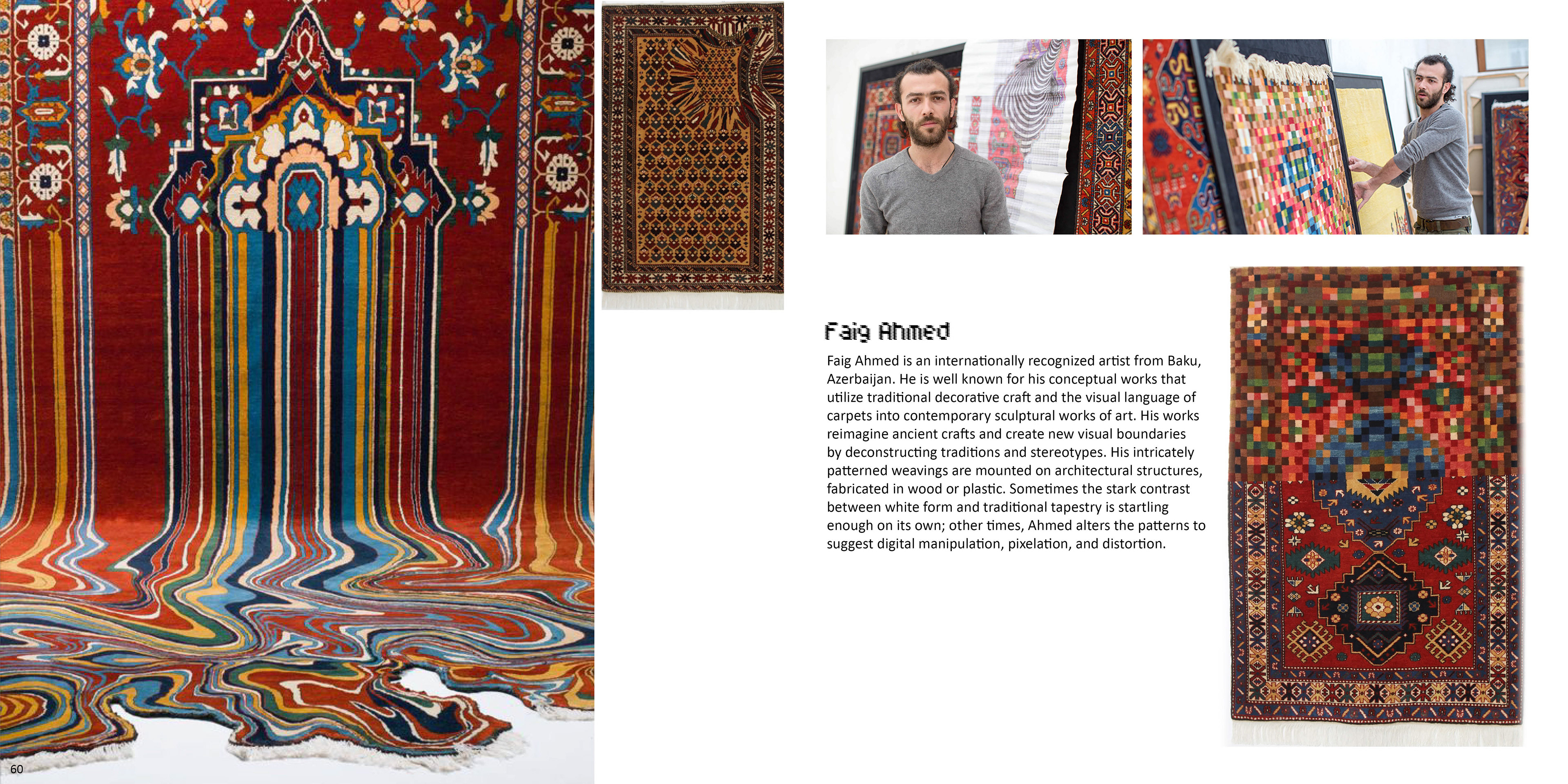
Phillip David Stearns
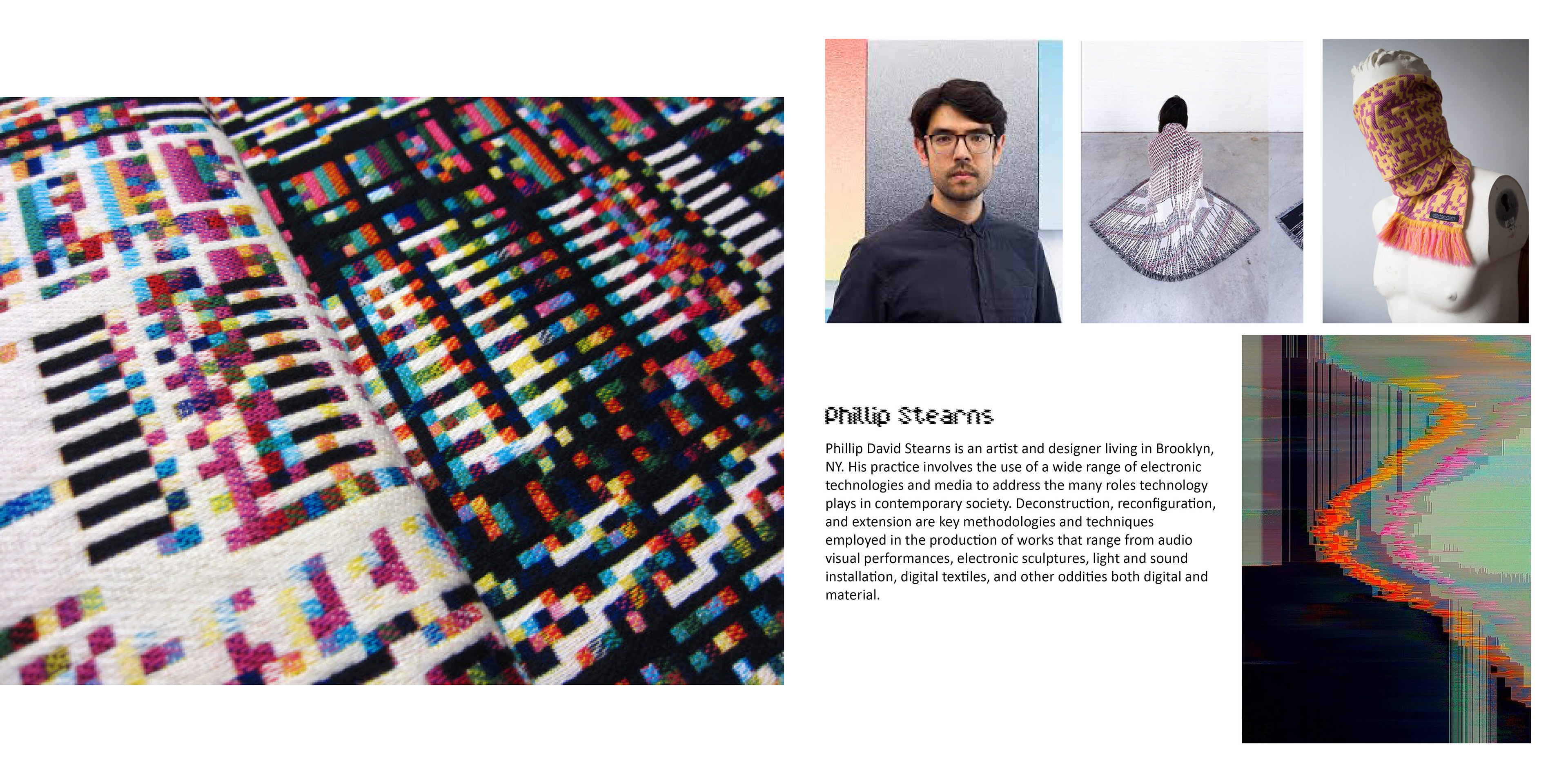
Benjamin Berg- stallio!
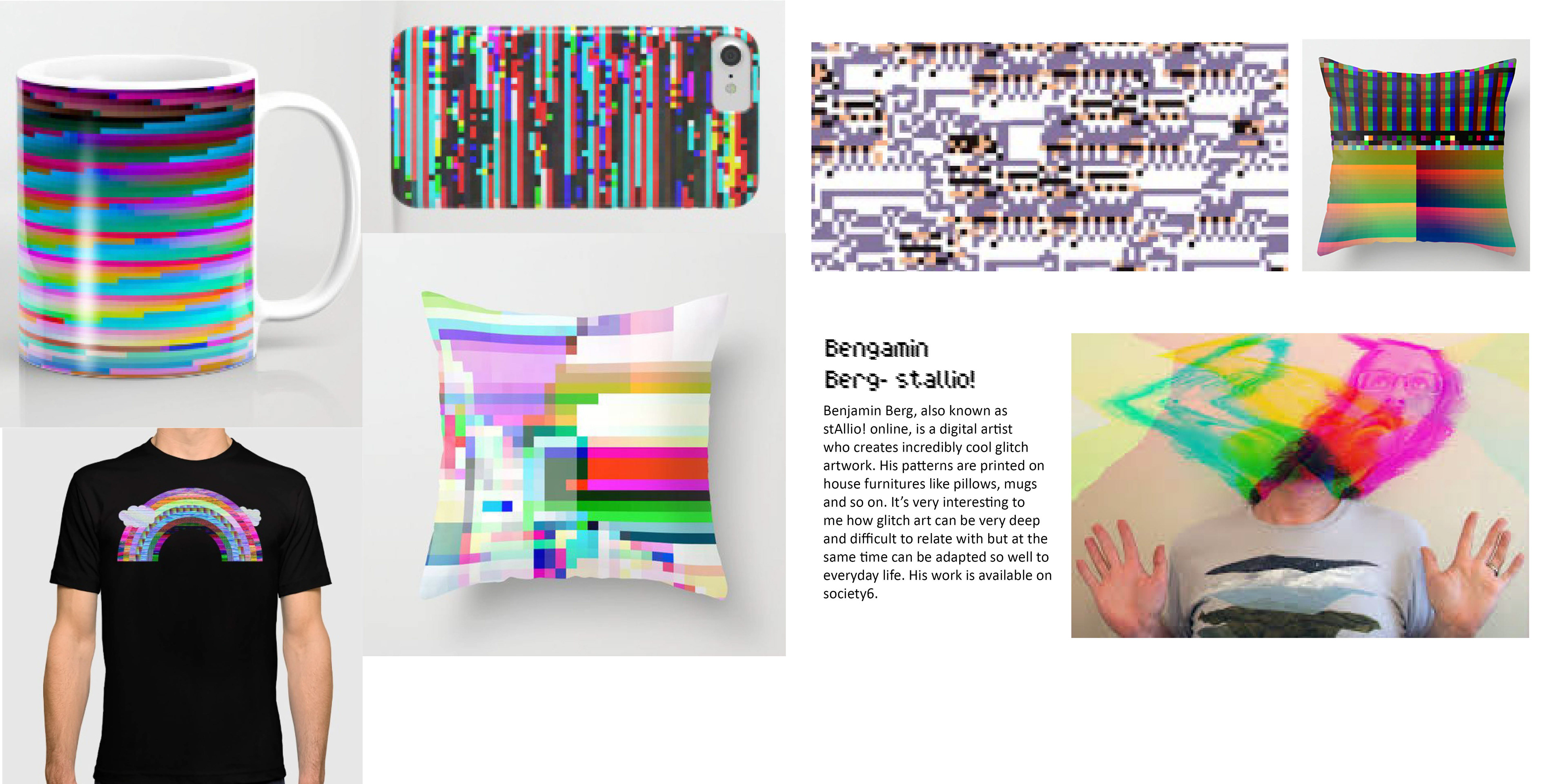
Ferrucio Laviani & Ucnv
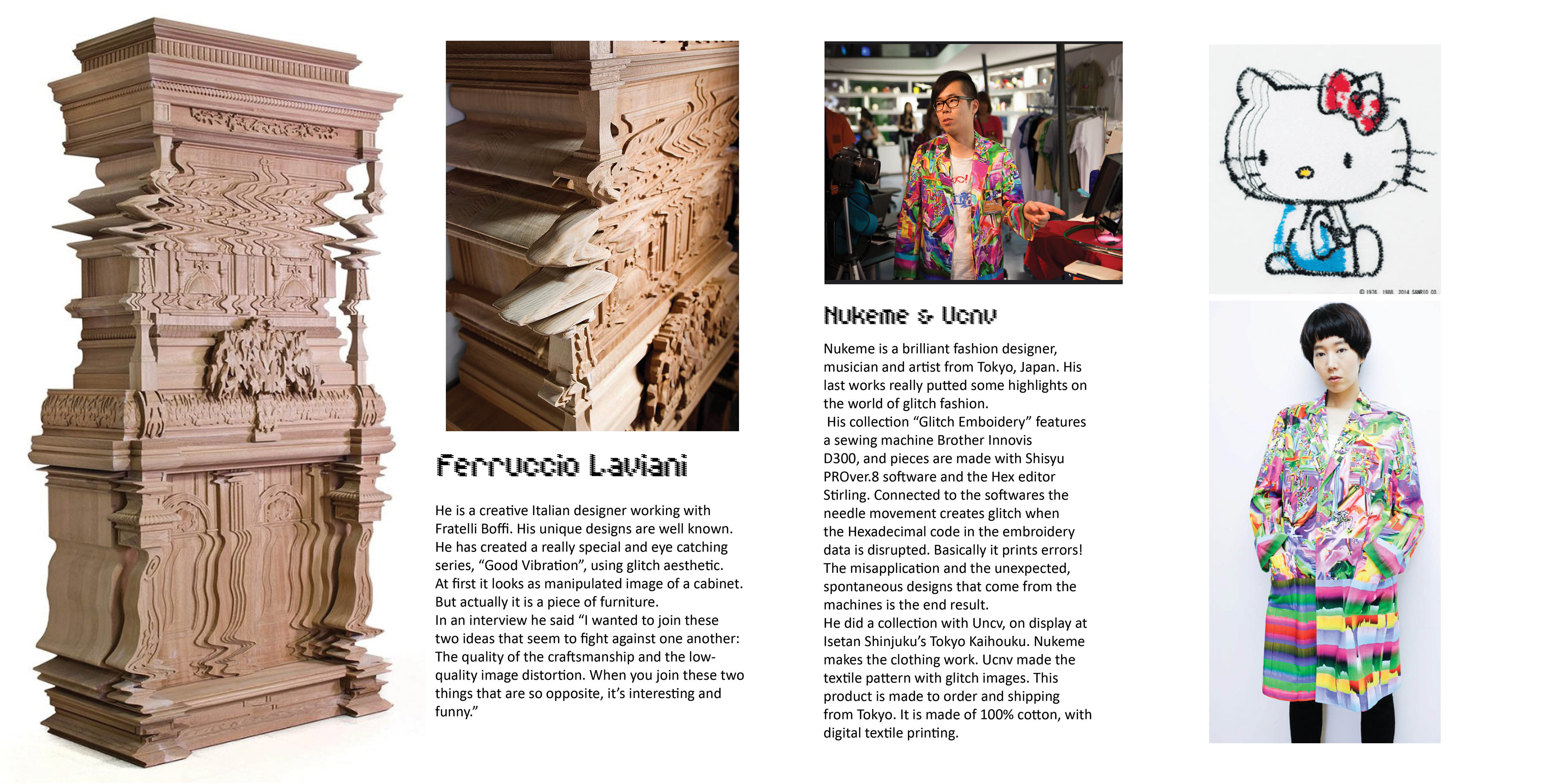
Brain storming
Motif Explorations
Fabric Sample development
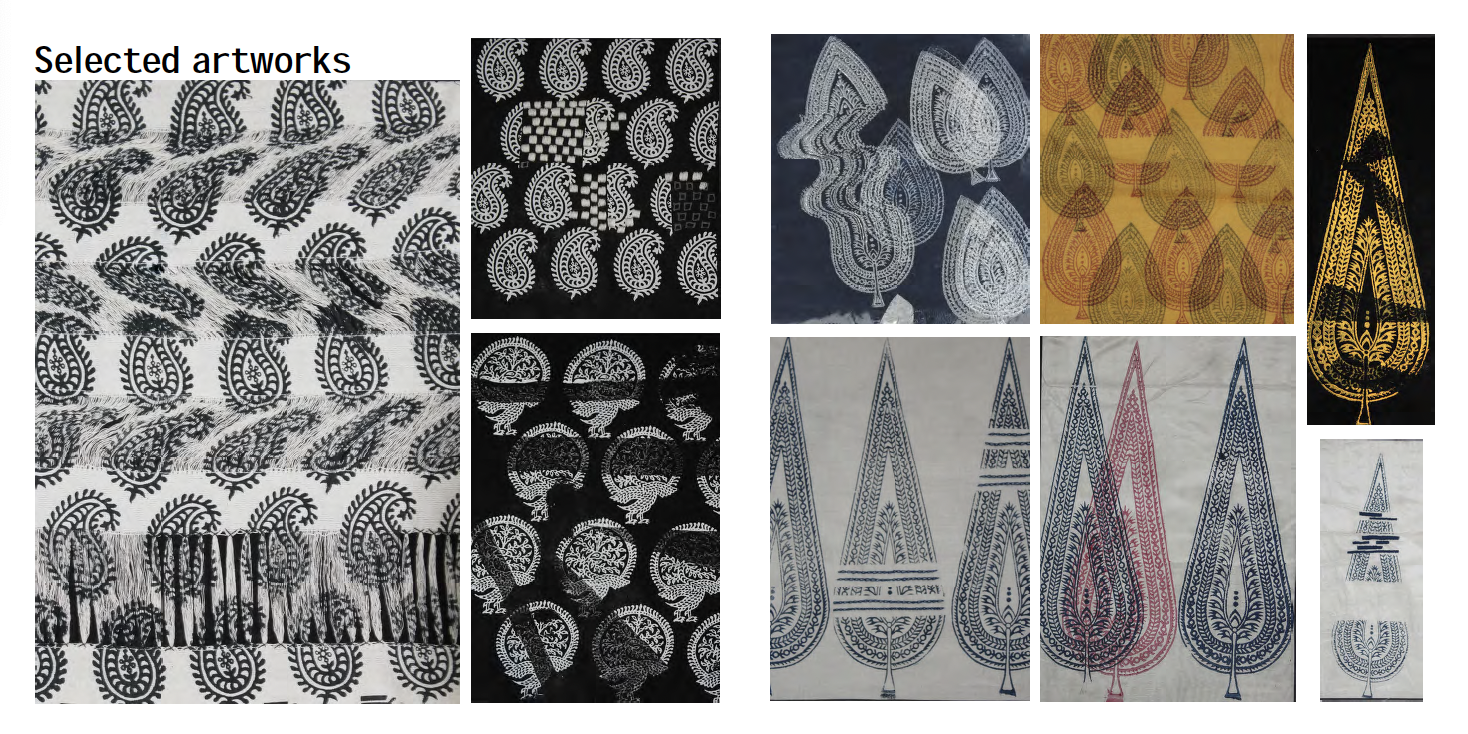
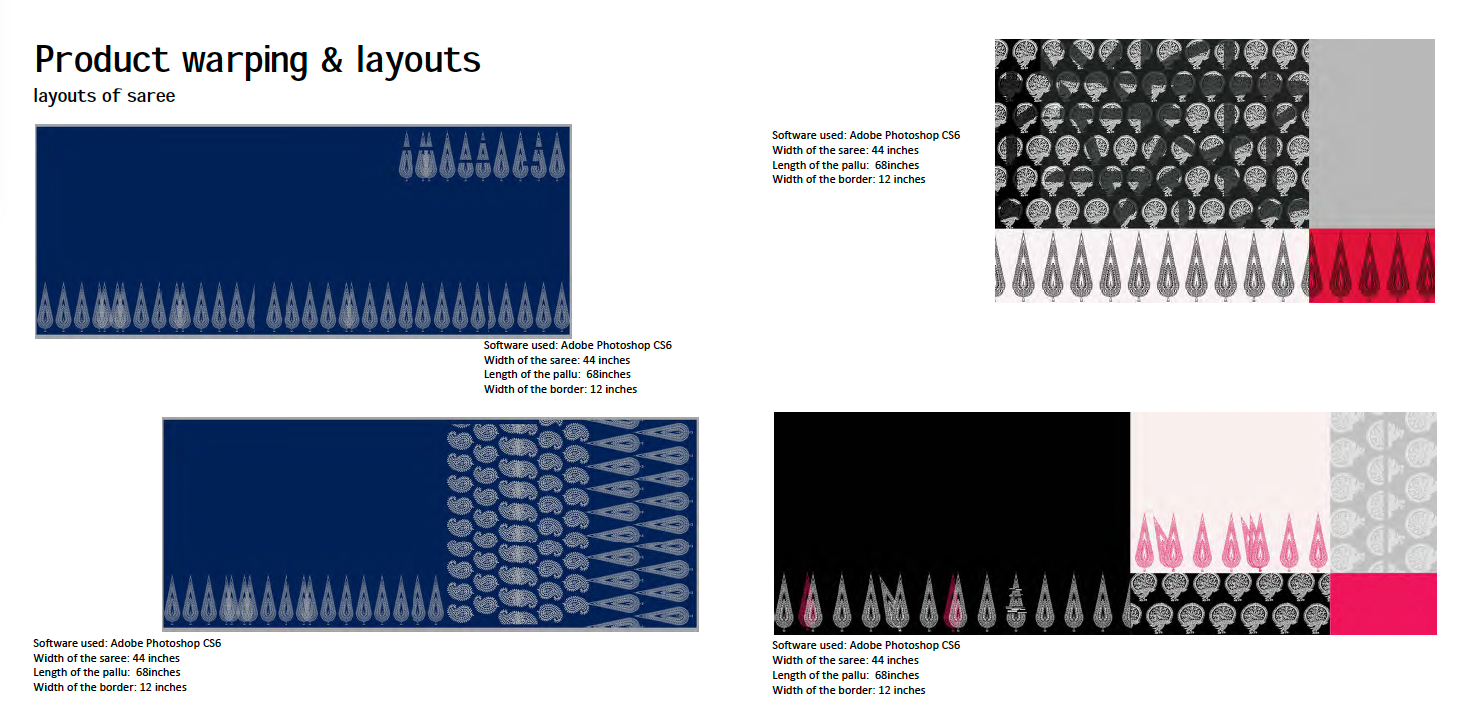
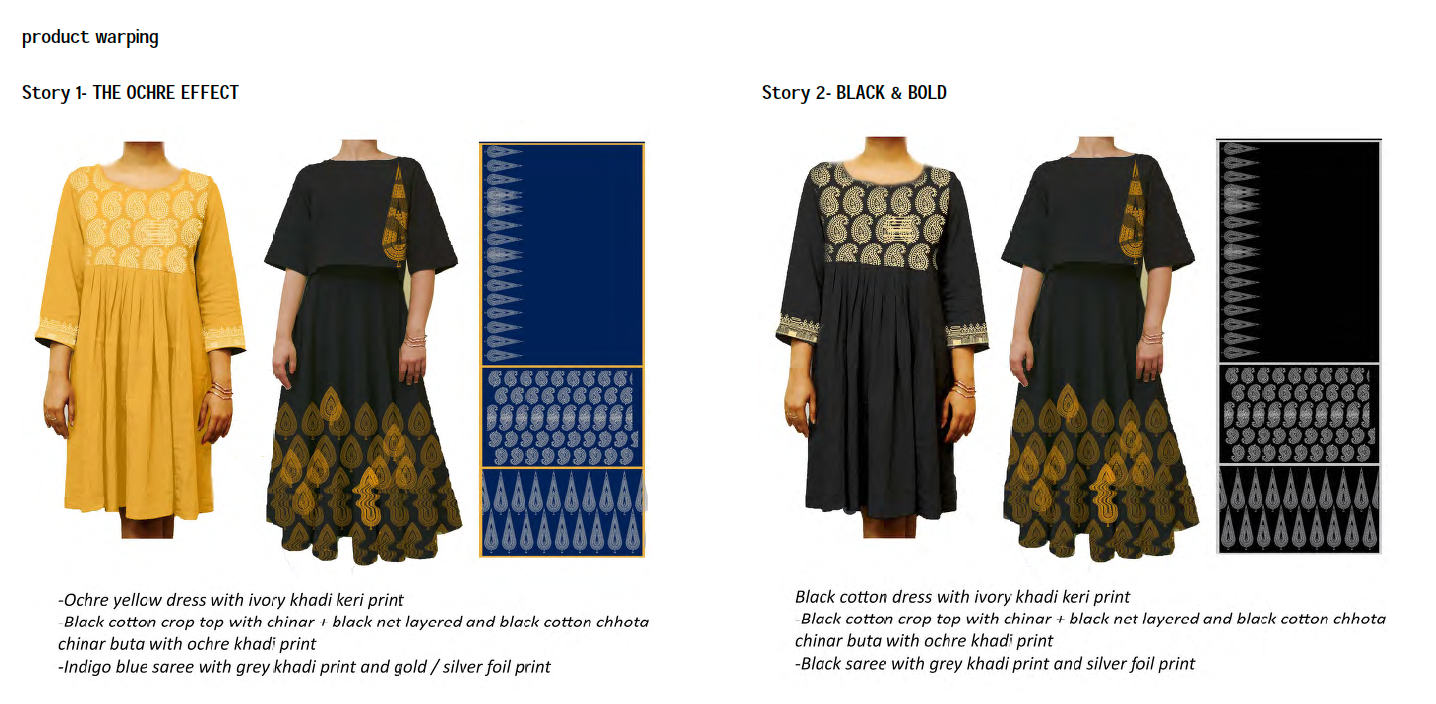
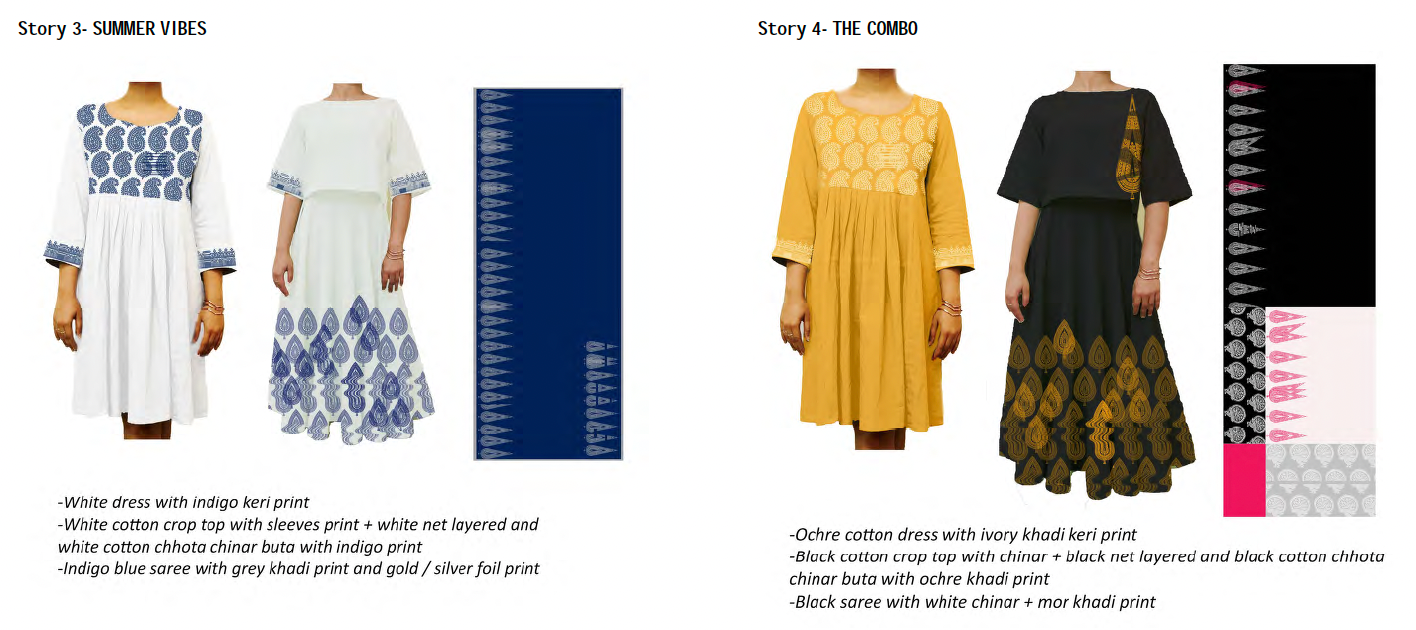
Conclusion
The graduation project has been an enriching experience, offering deep insights and practical applications that complemented seven semesters of learning. It provided a platform to delve into the fading art of Sanganeri block printing, sparking a passion for its revival. Despite limitations, the project successfully revived traditional motifs and highlighted the importance of understanding and preserving the craft's essence. The exposure to Sanganer's craft sector and interactions with craftsmen were invaluable, providing motivation and a deeper understanding of the craft. Networking opportunities and positive feedback suggest a promising market for the fusion of glitch art and Sanganeri block printing. This project has not only been a personal achievement but also a step towards preserving and promoting traditional crafts.
The graduation project has been an enriching experience, offering deep insights and practical applications that complemented seven semesters of learning. It provided a platform to delve into the fading art of Sanganeri block printing, sparking a passion for its revival. Despite limitations, the project successfully revived traditional motifs and highlighted the importance of understanding and preserving the craft's essence. The exposure to Sanganer's craft sector and interactions with craftsmen were invaluable, providing motivation and a deeper understanding of the craft. Networking opportunities and positive feedback suggest a promising market for the fusion of glitch art and Sanganeri block printing. This project has not only been a personal achievement but also a step towards preserving and promoting traditional crafts.
Glossary
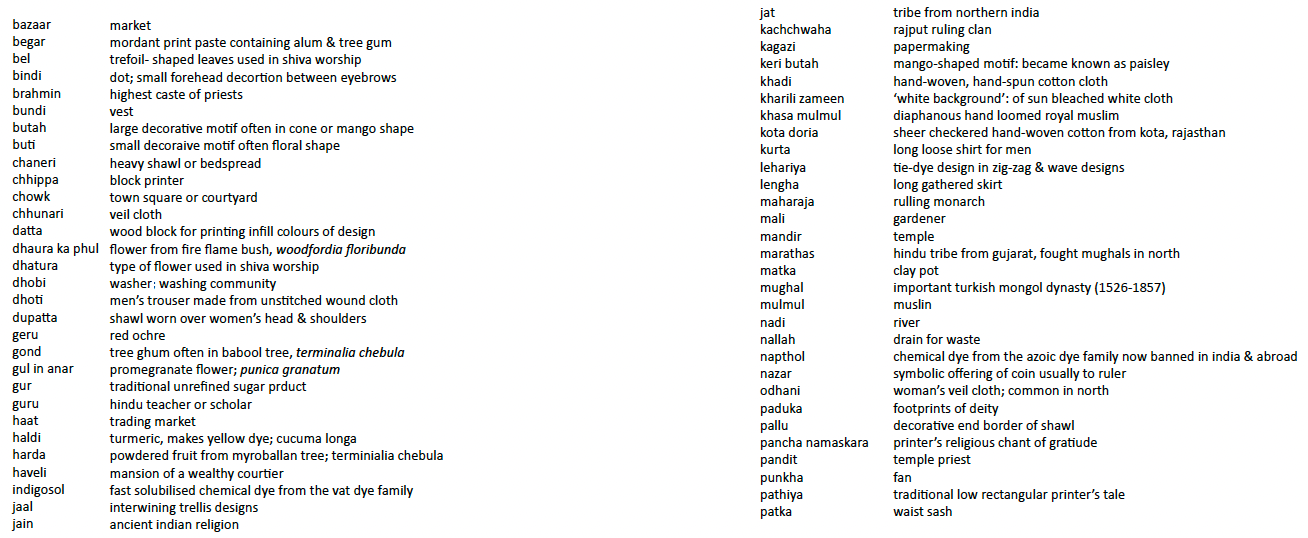
Bibliography
BOOKS
Singh, C 1979, Textiles and Costumes- From the Maharaja Sawai Man Singh II Museum, 1st ed. Textiles and Costumes- From the Maharaja Sawai Man Singh II Museum Trust, City Palace, Jaipur. Skidmore, S 2009, SANGANER traditional textiles~ contemporary cloth, 1st ed. AMHP Publications, Jaipur.
Mohanty, B & Mohanty, J 1983, Block Printing and Dyeing in Bagru, Rajasthan. 1st ed. Calico Museum of Textiles, Ahmedabad.
Moradi, I, Scott, A., Gilmore, J & Murphy, C 2009, Glitch: Designing Imperfections. 1st ed. Mark Batty Publisher, New York.
WEBSITES
Vidani, P. (2017). stAllio! on tumblr. [online] Stallio.tumblr.com. Available at: http://stallio.tumblr.com/ Accessed 10 Apr. 2017].
Studio Laviani. (2017). Studio Laviani. [online] Available at: http://www.laviani.com [Accessed 6 Feb. 2017].
Animalswithinanimals.com. (2017). stAllio! glitch video. [online] Available at: http://www.animalswithinanimals.com/bent/glitchvideo.html [Accessed 10 Apr. 2017].
Shaymoradi.com. (2014). REON, Shay Moradi’s Portfolio. [online] Available at: http://shaymoradi.com/?/projects/Reon/ [Accessed 7 Oct. 2016].
Phillip David Stearns. (2017). Phillip David Stearns. [online] Available at: http://www.phillipstearns.com [Accessed 10 Apr. 2017].
Faigahmed.com. (2017). FAIG AHMED. [online] Available at: http://www.faigahmed.com/#origin [Accessed 6 Feb.2017].
Glitch Textiles. (2016). [online] Available from: http://www.glitchtextiles.com/home [Accessed 7 Oct. 2016].
Gaatha.com. (2015). sanganer block printing process and history | Gaatha . गाथा ~ handicrafts. [online] Available from: http://gaatha.com/syahi-begar/ [Accessed 2 Jun. 2016].
BLOGS
Ferruccio Laviani, “Good Vibration” glitch design. (2015). [Blog] altervista. Available at: http://portraitch.altervista.org/ferruccio-laviani/ [Accessed 6 Mar. 2017].
Nukeme, “Glitch Embroidery” from Japan 2015. [Blog] PORTRAITCH. Available from: http://portraitch.altervista.org/nukeme/ .[18 July 2016].
Benjamin Berg, stAllio! and glitch art. (2015). [Blog] altervista. Available at: http://portraitch.altervista.org/benjamin-berg/ [Accessed 6 Feb. 2017].
WAKELIN, N. (2015). Pixellated Hair Is A Wild Look. [Blog] Fashionably Geek. Available at: http://fashionablygeek.com/design/pixellated-hair-is-a-wild-look/ [Accessed 2 Jan. 2017].
VIDEOS
Leveritt, T. (2014). Glitch textiles. [video] Available at: https://www.youtube.com/watch?v=H_Qs6GC2Z2A [Accessed 8 Nov. 2016].
Dredge, J. (2017). SFXC Hydrochromic Wet and Reveal Screen Ink. [video] Available at: https://www.youtube.com/watch?v=2MH3wjm9CVo [Accessed 5 Oct. 2016].